At Midwest Tungsten Service, we pride ourselves on crafting a diverse array of specialized machined parts. To achieve precision and excellence, our engineers and machinists design and create custom machines, fixtures, and tooling tailored to meet intricate customer requirements. Our production approach utilizes a blend of automated, continuous, discrete, and batch process manufacturing to ensure top-notch completion of customer orders.
An essential component of our operation is the part processing team, spearheaded by Ana. This dedicated team is pivotal in the crafting of our tungsten filaments. For instance, in one filament process, we employ a batch method to meticulously cut and coil the wire, after which a team member, with precision tooling, fashions two distinctive bends on the filament's right side. See below.
Certain filaments require the application of heat during bending operations. This heating enhances the wire’s ductility and protects the filament's structural integrity. Some of our most intricate filament designs necessitate multiple unique tooling sets to introduce additional bends.
Ana’s team takes care to maintain quality control during these operations. They monitor for errors originating from batch processing and previous bending operations. Parts are frequently checked for adherence to customer specifications.
Beyond Ana’s primary role in this department, she also works cross-functionally with other teams, lending her expertise and skills to inspection, parts cleaning, and packaging.
When Ana steps away from the world of tungsten, she cherishes time with her daughters, challenges herself with rigorous bootcamp-style fitness routines, and enjoys strolls with one of her two canine companions. (Her second dog prefers a leisurely lounge over a brisk walk!)
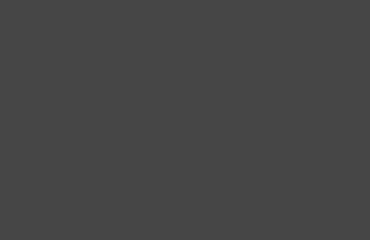