Originally Published 8/31/22
In this post, we go behind the scenes by interviewing Ron who has been an integral part in the success of Midwest Tungsten Service throughout the years. We sit down and get insight into his role and his key contributions the the company. We also get an understanding of his background and get to know him outside of work.
1. What is your Name/Job Title?
Ron-Design and Manufacturing Engineer
2. How long have you been with MTS?
I’ve been building tools, machines, and finished parts with MTS for 30 years. When I began with MTS, I was responsible for building machine tools. As MTS expanded, I took on additional responsibilities, including designing machines and producing machined parts. Presently, I manage the entire machine shop which includes overseeing and training other machinists.
3. What influenced you to get into machining?
My best friend since 7th grade was familiar with machining, as his uncle owned and worked in a machine shop. He suggested I go to school for machining and make a career of it because it is a rewarding and good paying career. I took his advice and received my education for machining and engineering at College of DuPage. Before working at MTS, I was a machinist, setting up and operating machine tool equipment with an in-depth knowledge of how the machine works.
4. What do you like most about your role?
I love building things. At MTS, every day is different with new challenges. I enjoy the latitude of being creative and innovative in my position.
5. What does a typical day consist of?
I usually begin by checking work orders for jobs which require machining parts for customers or modifying existing parts. I may be required to do CAD modelling for some of these jobs. I assign jobs to other machinists to work on. When needed, I also run certain specialized machines in our shop. I also work with the inspection team in our wire forming area. I may also be designing or building customized production equipment for our shop.
6. What characteristics make for a good design engineer?
Creativity, as many machines begin as concepts and are custom built from scratch. Curiosity, for understanding how things are made and how they work together. Confidence and perseverance, since the building of the machines is a complicated process, and you must always feel like you will persevere and never sell yourself short. Problem solving, I start by taking a project and break it down to a simple, manageable, process steps.
7. What type of machines do you use for your role?
I use the Fanuc Wire EDM Machine which cuts metallic material or material that conducts electricity using electrical discharge. The EDM works well for machining precise parts from hard materials like tungsten. I also use Miltronics Machining 4-Axis Center which is used for milling and drilling. In addition, I use our Okuma Turning Center that is used for machining round parts. Our machine shop has many other machines as well, such as water jet cutters and EDM drills, but those are what I use most often.
8. What challenges do you enjoy when it comes to working with tungsten?
I enjoy working with tungsten because it requires a unique skill set. It takes a different thought process to work with it compared to other metals. It behaves differently and you can’t treat it like most average metals. I have worked with titanium (tough to machine) in the past which is the anti-tungsten. With tungsten, you must be diligent in the set up because tungsten has less room for error. We pride ourselves on our low scrap rate with our expensive raw materials. With tungsten your approach must be intentional. You need to have the entire process mapped out before you begin.
9. What are some insights about tungsten and other metals used by MTS that many people may not know?
Tungsten is unique as it has high strength at elevated temperatures. It retains strength properties at high temperatures and has a very dense structure. It’s quite heavy for its size, having a density about 75% greater than that of lead. Tungsten can’t be extracted and refined under conventional methods. It is extracted chemically from ore to pure tungsten powder, then pressed and sintered into bars that are densified with heat and mill work. It is then annealed to release stress to keep it somewhat malleable. Pure tungsten’s metallic structure is crystalline which makes it both brittle and hard. I like to machine using the EDM (Electrical Discharge Machine) as it is accurate and reliable even on such a difficult material.
10. What do you like about training new machinists?
My favorite part is passing on knowledge. I like to teach and pass on information and experience, which is great to have others understand what I have learned. I can give a piece of myself to others and pay it forward.
11. What project are you most proud of at MTS?
The project I am most proud of is a machine which automatically forms tungsten evaporation filaments under high heat using spooled tungsten wire as an input. I designed and built that machine from scratch. It is programmable, which allows the machine to set itself up based on input from the user or from pre-programmed parameters. It took about a year and a half to engineer, build, and program.
12. What do you like to do in your free time?
In my free time I like to do a lot of home projects.
I am also passionate about aircraft. I built an experimental airplane (Velocity XL) by hand which took 12 years to build. I love the process of building things and I truly believe “it’s about the journey not the destination”. I love the notion of “work in progress” as I like to revisit and enhance projects I have worked on previously.
Along with building aircraft, I am also a single engine general aviation pilot. I have flown 152, 172, 182 Cessna aircraft, Piper Warrior and Piper Archer aircraft. I enjoy taking my airplane on short trips which is one of my favorite hobbies.

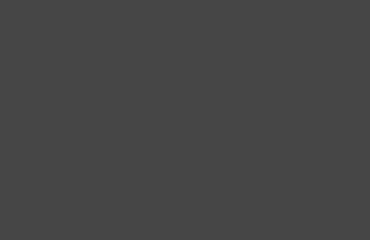
Related Tips
MTS Owners Featured in Crain's Chicago Business
MTS Owners Featured in Crain's Chicago Business
